Avoiding air problems
Air elimination through the last couple of decades has changed dramatically. Four or more decades ago, we had the circulator(s) located on the return piping of the boiler and air elimination was done by a B&G Airtrol fitting, pictured Below, mounted on the supply pipe with a dip tube into the boiler. The dip tube was low enough in the boiler that no air got into the supply piping. There was a bell looking fitting the dip tube came out of that collected the air went on to a ceiling mounted expansion tank. There were purge valves installed for zone purging of air when the boiler was installed or if the system needed draining for service. This application worked very well.
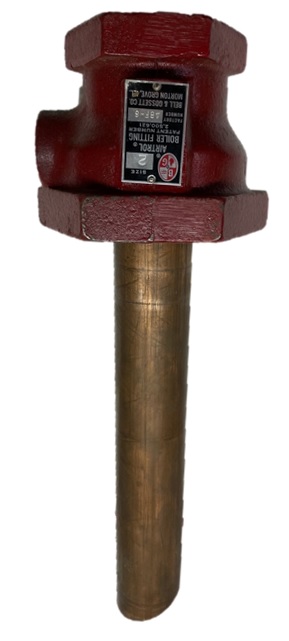
As the boiler industry evolved we did away with the air did away with the air control fittings with dip tubes and added automatic air vents and air separators. We still added purge valves for purging the air pond boiler installation or system service. At this point people started adding automatic air vents with non-diaphragm type expansion tanks. This created a problem of having a non-maintenance style tank to a tank that needed draining.
As we continue to move forward with air elimination from hydronic systems about 1958 the manufacturer suggested moving the circulator from the return side to the supply side of the system. The reason for this is credited to the introduction of a one-piece circulator. Prior to the one-piece circulator we had three-piece circulators. The three-piece circulators could move much more water for its size than the one-piece circulator.
Let's look at a drawing when the circulator is not running. If there is no pump operation water pressure would be the same at any given altitude in the system. For instance, if we measure four feet from the floor and the water pressure is 14 PS I any of the system piping four feet off the floor would have 14 PSI. If we measure 15 feet off the floor and the pressure at that point would be 6 PSI any pipe at 15 feet off the floor would be 6 PSI.
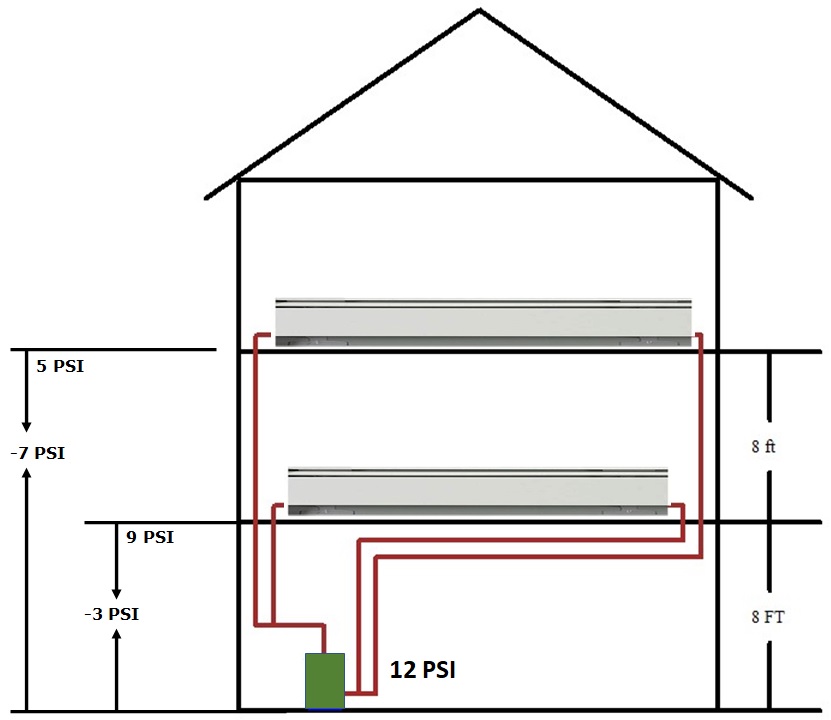
When a circulator is running the pressure on the outlet side will always be higher than the inlet side of the circulator. The point where the expansion tank is connected to the system is called the point of no pressure change. This simply means if the system fill pressure was 12 PSI that pressure will always be 12 PSI unless we raise water temperature, drop the water temperature, manually fill, or drain the system. So, if the pressure does not change at the expansion tank connection the circulator can add system pressure or drop system pressure. The simple rule is whatever side of the circulator the expansion tank is on the pressure on that side of the circulator does not change.
Circulator installed on return piping
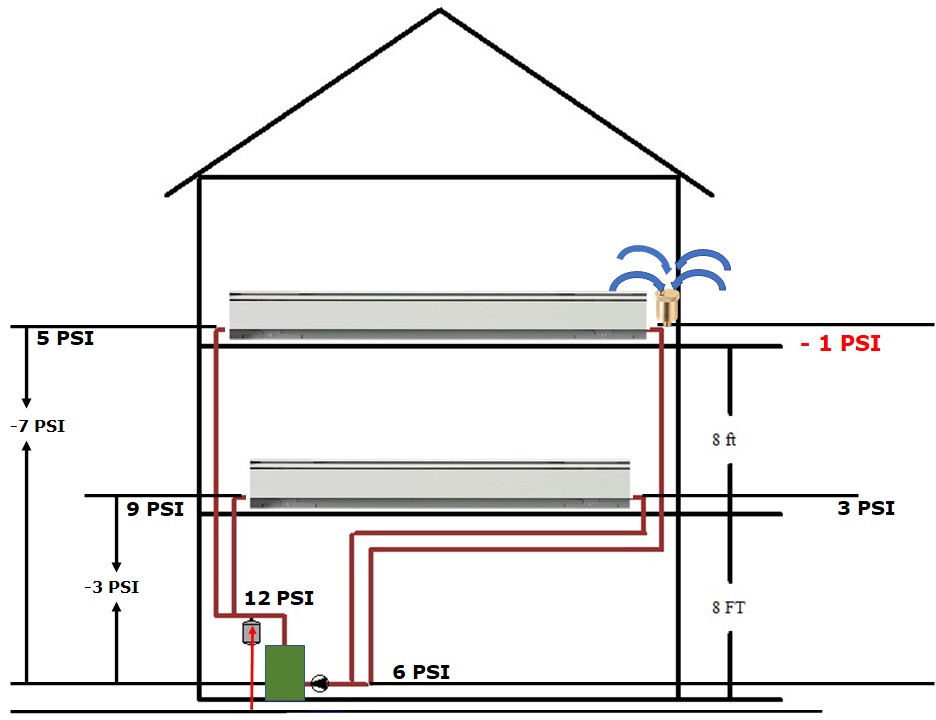
Installing the circulator on the supply pipe after the expansion tank connection means the inlet to the circulator would remain at 12 PSI with a 12 PSI fill pressure and the discharge pressure would be increased adding pressure to the system. Depending on the size of the circulator we could add 50% or more of the system fill pressure.
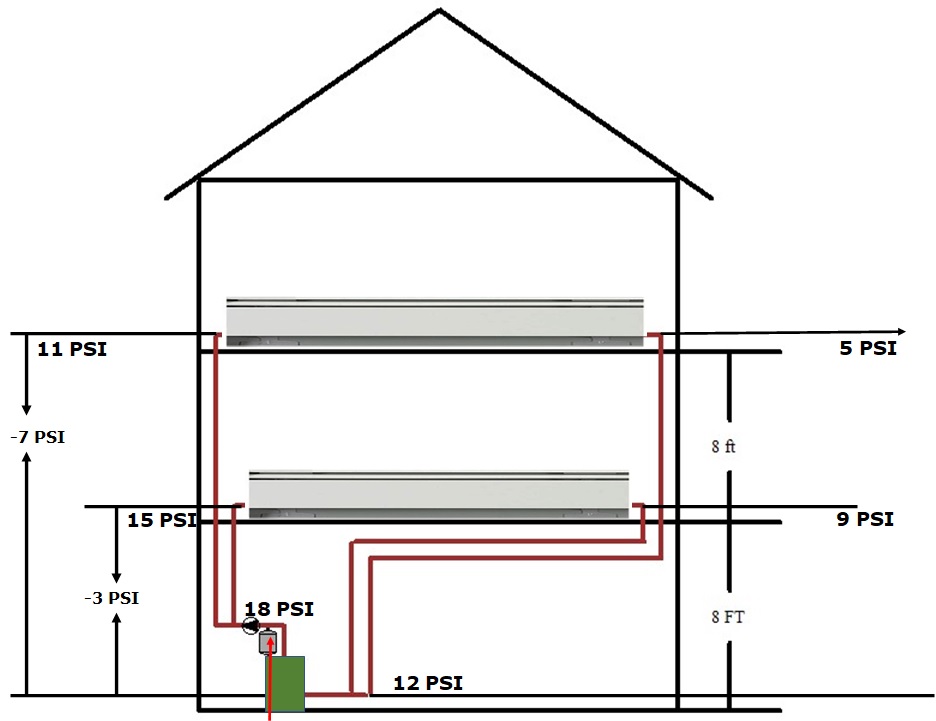
Automatic Air Vent Information
Automatic air vents were introduced in the mid to late 1950s. This was a good idea and a bad idea at the same time. The good idea was they were required when they introduced the bladder style expansion tanks, and a bad idea when installed on non-diaphragm ceiling mounted steel expansion tanks. You will hear automatic air vents called hy-vents, barrel vents, can vents and maybe some others names I haven't heard of. I will call them auto vents for short.
You will find auto vents all over the system. I've seen them right at the boiler, at the high points of the system, on stamp pipes where the returns and supplies are in the basement, and inside of cabinet convectors and baseboard covers upstairs. I have seen these vents create problems as they leak or spray water over time. I've seen damage to wooden floors, rusting radiation covers, damage to walls, etc.
Today with the use of better air separators and one-piece circulators that can add a little more pressure to the system fill pressure auto vents anywhere in the system are not really required, fact they can be detrimental. If a vent can automatically vent air, they can automatically suck air in under other conditions. Let's assume, they feel pressure on the system is 12 PSI and the circulator is on the return side pumping toward the expansion tank connection and when the circulator starts it can drop the pressure low enough for the high vent to draw air in. After the circulator stops the air that got drawn in can be vented back out, but some of the year has mixed with the water and gone back down to the boiler.
It is best to do all air elimination at the boiler taking advantage of the extra pressure added by the circulator when pumping away from the expansion tank connection.