Common Mistakes made with Primary/Secondary (P/S) Piping
The problem I’ll be discussing is using a boiler primary loop and not installing close spaced tees for each zone. Instead, the installation has all zone supply pipes and all the zone return pipes somewhere after the supply’s. This is a bad attempt of trying to blend primary secondary piping and manifold piping together. The only thing accomplished is eliminating hydraulic separation. This in many cases causes ghost flows. Unfortunately, when pointing this out on a jobsite the response one normally hears is, “I do this all the time and never had a problem before”. Well Bucco, you have the problem now. You really had it before but not bad enough to show up. When the conditions are right, it does show up to the point is becomes a noticeable problem. Since you never got the complaint before does not mean it was not happening but in this application the resistance or flow in one loop is much different than another loop. Not only is the consumer overheating a given zone, but his attitude is also being heated, good thing he does not realize he has a higher fuel bill. The main reason this does not work is there is no hydraulic separation between the boiler primary loop circulator and the zone circulators. If your not sure what I mean take a look at the Primary Secondary Basics page from the menu on the left or purchase the primary secondary seminar where it is explained in much more detail. Here are four reasons for the ghost flows in the system.Problem #1
- Zone circulator could be too large for a given zone
- Boiler primary loop pipe is undersized
- Boiler primary loop circulator is undersized
- Little resistance on a micro-zone.
The given here is there are working flow checks or check valves on the zones.
The zone with the ghost flow is moving water up through its flow check valve, through the zone, down the return and back to the zone that is needing the extra flow.
Below the arrows are showing the ghost flow that is being created by the larger zone.
How do we fix this? Here are two solutions.
- Remove all the returns from the bottom of this loop and put a return tee after each zone supply tee. Note, the flow from the boiler primary loop must enter the zone supply tee first and return as close as possible after the zone supply tee. The orientation of the zone return tee can be fed from the bottom. The idea that the supply tee points up and the return tee points down is not an issue. Be aware piping this way could create a new problem. As the number of zones increases the supply water temperature to the latter zones will be tempered down due to blending return in the boiler primary loop from prior zones running.
- Cut the boiler primary loop on the right side on this drawing and cap the two pipes to create a supply manifold and a return manifold. But wait we are not done. Now on the left side of the drawing cut the pipes and tie the two pipes together so the supply and return manifolds are one pipe. Insert two closely spaced tees and pipe the boiler into them creating hydraulic separation between the boiler loop and the system loop making sure you move the circulator to the boiler loop. There is no need to have a circulator added to the system side of the piping as each zone has its own circulator. Problem solved and lesson learned.
Problem #2
Putting a 1-1/4” elbow between the tees will add about 3 EFP. A valve could add up to 10+ EFP.
Problem #3
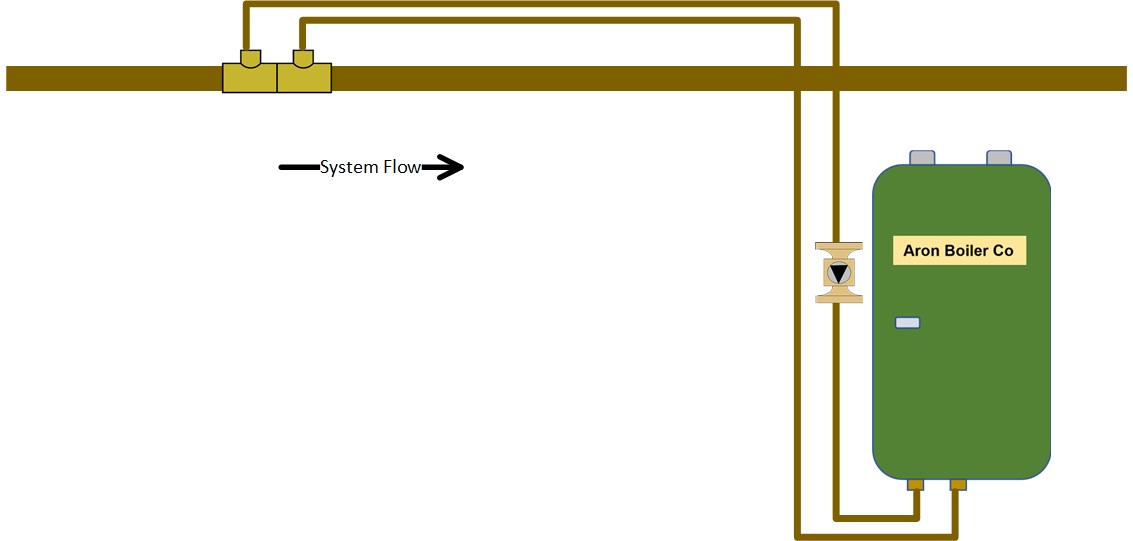
We decided to shorten the highest horizontal runs and the problem went away.
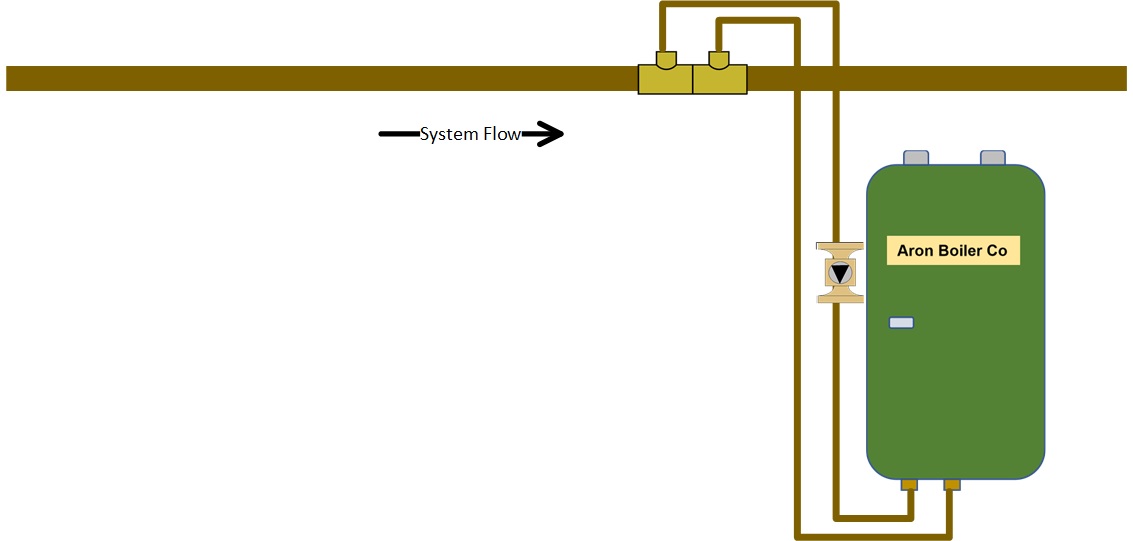
Bring the secondary boiler piping into the side or the bottom of the primary pipe.Do not chance having these problems.
Problem #4
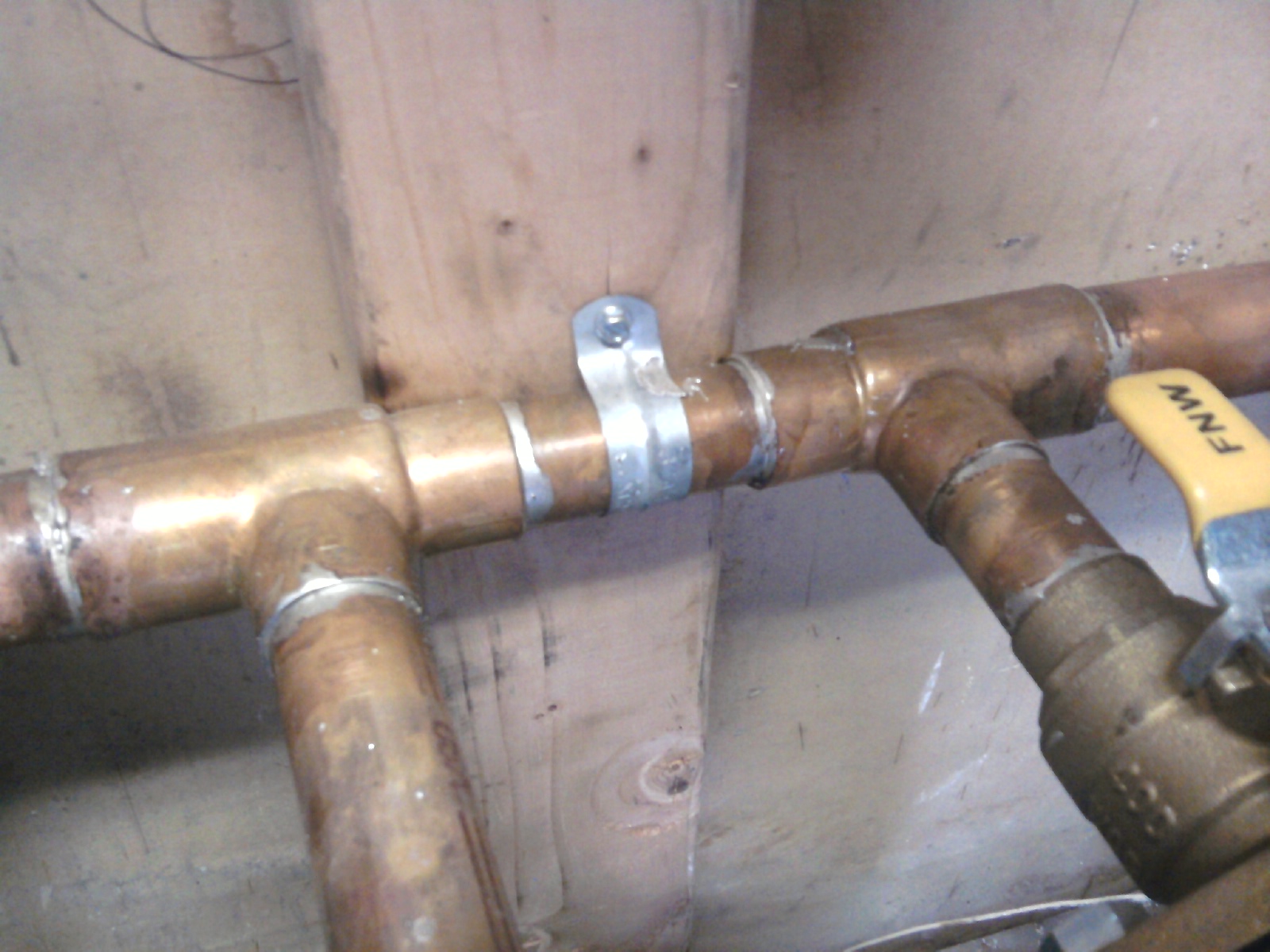
Problem #5
One of the more common problems I experience is one of the tees is rotated 90 degrees. This changes the flow in and out of the secondary zone be it the boiler or a heating zone. As stated above we are looking for a very low pressure drop between the tees. We need the same resistance into the secondary zone as we have out of the secondary zone. If you read the P/S tutorial you know the maximum distance between the tee branches or also called the bull of the tees is not to exceed 4 times the diameter of the primary pipe not to exceed 12” whichever is closer. What is the problem with this first drawing?
Since every fitting has an equivalent feet of pipe (EFP) plus all the piping the water passes through is a resistance to flow, this can create a problem. Since the secondary loop is always piped away and returned to the branch of the tees, we need to take a look at the EFP of the tee. See the EFP chart link on this page, but if we look at 1-1/4” tees we can see the flow into the tee and out the branch is equal to 5.5 EFP. Remember we need the same resistance into the secondary zone as we have out of the secondary zone to keep the flow correct. The flow into the tee and straight through the tee is 0.6 ft. of pipe. What this means is one tee route is 5.5 EFP and the other tee route is 0.6 EFP. The result is unbalanced flow. In the above example, we can measure the distance and if it measures with a rule to 5” we might think we are OK. But looking at the EFP we are about 6 feet of pipe.
Disclaimer: The information found on this website is for informational purposes only. Any preventive maintenance, service, installations should be reviewed on a per job situation. Any work performed on your heating system should be performed by qualified and experienced personnel only. Comfort-Calc or its personnel accepts no responsibility for improper information, application, damage to property or bodily injury from applied information found on this website as it should be reviewed by a professional.